Case Study: Downer Utilities
Empowering a new approach to safety
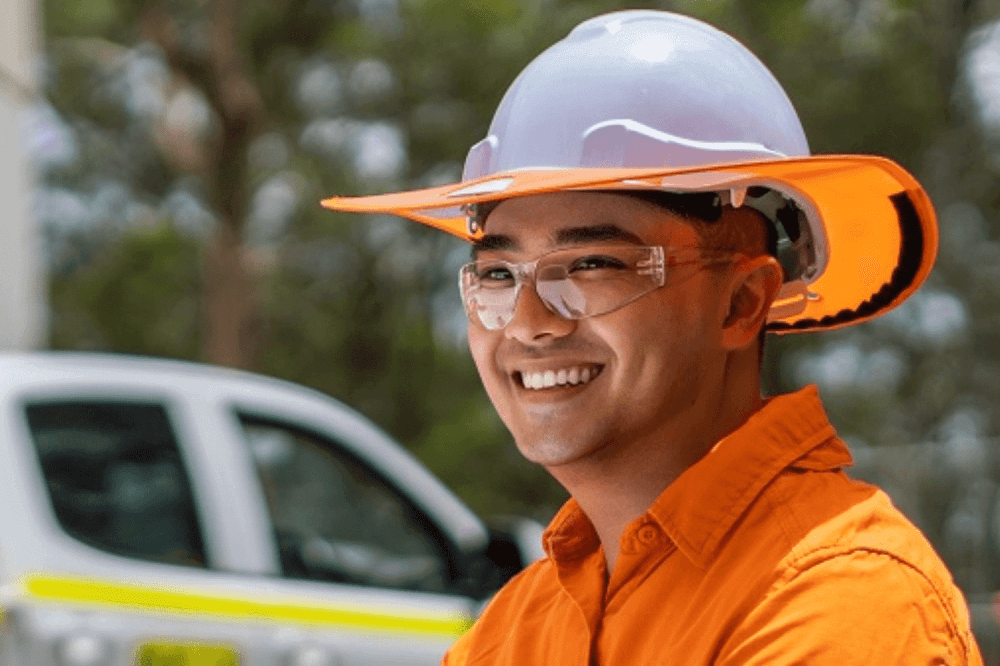
Starting in early 2018, Downer Utilities embarked on a journey to rethink its approach to safety, evolving from traditional, risk-centred methods to a more dynamic, holistic strategy. With strong leadership support, Downer began integrating Human and Organisational Performance (HOP), Safety II, high-reliability practices, and resilience engineering into its framework. This shift aimed to create an environment where employees could engage meaningfully with safety, feel empowered to contribute ideas, and even grow from their work experiences.
The approach prioritised working with early adopters—teams who were open to experimenting with new methods. By focusing first on these groups, Downer could demonstrate real results and build compelling examples of success, gradually inspiring broader acceptance across the organization. This leadership-driven strategy laid the foundation for a people-centred safety culture, where frontline insights were valued and employees felt supported in actively contributing to safety improvements.
With a focus on flexibility, inclusiveness, and continuous improvement, Downer has created a safety culture that aligns with real-world conditions and adapts to operational needs, setting an industry standard for a safer, more collaborative workplace.
People as the Solution, Not the Problem
A key principle in Downer’s approach to safety was recognising employees as essential to the solution rather than merely enforcing compliance. This people-cantered strategy acknowledged that employees have invaluable insights into the practical realities of their work. The organisation recognised that safety systems should empower individuals to navigate and mitigate risks in ways that align with their daily responsibilities.
This shift enabled Downer to build a supportive work culture by focusing on adaptable systems that prioritise human strengths and needs. As Downer’s Safety Innovation Lead at the time, Michelle Oberg, explained, “It’s all about systematically supporting our people so that they’re set up for success regardless of their personal circumstances on any given day.” This approach allowed Downer to go beyond compliance, creating a work environment where employees were genuinely empowered to participate in safety efforts and actively shape safer work practices.
Their commitment to viewing employees as active contributors helped build trust and engagement. Employees were encouraged to contribute ideas, address potential risks, and engage in problem-solving, fostering a workplace culture that valued their perspectives and recognised their role in enhancing safety.
Practical Tools: Learning Teams, Work Insights, and Local Experiments
Two primary tools helped bring Downer’s new approach to life: Learning Teams and Work Insights. Learning Teams brought together employees to discuss safety both proactively and after incidents, helping uncover real-world insights from daily work. Work Insights, developed in response to feedback, evolved from “appreciative investigations” and allowed Downer to gain a wider understanding of the challenges employees faced regularly. These tools provided a realistic picture, guiding meaningful adjustments to reflect the actual work environment.
Teams also used small-scale experiments, or “micro-experiments,” to test new safety initiatives locally before wider implementation. For example, their utilities division found that replacing standard paperwork checklists with interactive team conversations significantly improved safety engagement. This hands-on, adaptive approach allowed leaders to learn quickly from real feedback and adjust safety practices based on what genuinely worked for each team.
Downer’s approach was designed with adaptability in mind, ensuring that safety practices could evolve alongside the needs of employees and operational demands. Through a continuous improvement mindset, those leading the transformation within the organisation frequently revisited their strategies, adjusting based on direct feedback and new challenges faced in various areas of the business. By encouraging this flexible, learning-oriented approach, they not only minimised change fatigue but also kept the workforce engaged in safety initiatives that felt both relevant and sustainable.
Reinforcing the Safety Message
Downer recognised that changing culture required consistent messaging and communication across all levels of the organisation. Messages were repeated in different formats and venues to reinforce Downer’s new approach to safety. Michelle Oberg, Downer’s Safety Innovation Lead, emphasised the importance of repetition, noting that “it often takes hearing a message several times for it to truly sink in and become part of daily practice.” By keeping safety messages clear and frequent, they effectively communicated a vision of a safe, supportive, and adaptable workplace.
Engaging Delivery Partners in Safety Initiatives
Downer’s safety approach extended beyond its immediate employees to involve subcontractors—referred to as “construction and delivery partners.” These partners were invited to participate in Learning Teams, where they could share insights and help shape safety practices. Downer also included the same partners in the monthly Safety Climate Pulse surveys to strengthen its commitment to a collaborative and unified safety culture. These inclusive initiatives ensured that safety remained a shared goal, deeply rooted in its operations.
Freedom within a Framework
A unique element of Downer’s safety transformation was its “freedom within a framework” approach. While foundational safety requirements remained consistent, employees were encouraged to make decisions within these boundaries, allowing for innovative, practical solutions tailored to real-world conditions. This structure gave employees the confidence to apply their insights within a clear framework, fostering a more agile and resilient safety culture that responded well to both day-to-day and longer-term needs.
Positive Outcomes and Key Takeaways
Downer’s approach led to greater employee engagement and open communication around safety. Employees felt empowered to share valuable ideas and insights, resulting in a collaborative environment that naturally supported compliance and operational improvements. By embracing adaptability, Downer built a safety culture that evolved with employee feedback, operational needs, and a continuous improvement mindset.
In implementing these changes, those leading the approach learned that building momentum with early adopters was key. While initial efforts focused on persuading everyone, the company found that working with enthusiastic teams first helped build a compelling case that eventually inspired others. Gathering baseline data also proved invaluable, enabling Downer to track improvements, demonstrate clear evidence of progress, and refine practices through micro-experiments that catered to diverse teams.
Ultimately, Downer Utilities’ safety journey created a workplace where safety practices were seamlessly integrated into daily routines and flexible enough to adapt to new challenges. By emphasising a balanced approach that included structure and autonomy, the organisation has fostered a safety culture rooted in inclusiveness, empowerment, and sustainable operational excellence, setting a benchmark for others in the industry to follow.
Adapted from the HOPLAB Collaboration Webinar with Downer Utilities’ Michelle Oberg: Setting people up for success